آشنایی با گیربکس های صنعتی و کاربرد آنها در صنعت
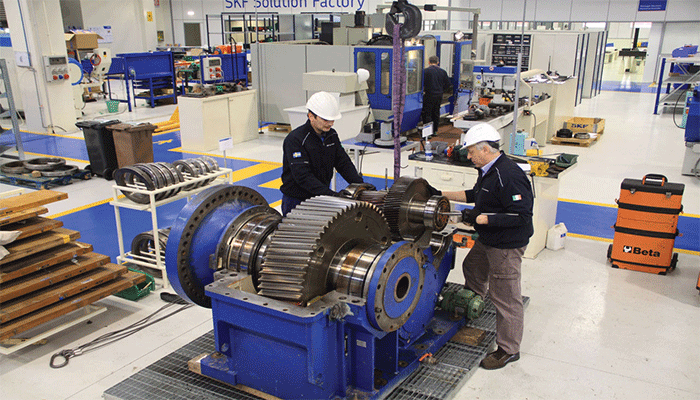
آشنایی با گیربکس های صنعتی و نحوه عملکرد آنها به عنوان یکی از قطعات پرکاربرد و مهم در دستگاههای صنعتی امری ضروری است. گیربکسهای صنعتی قطعاتی جهت ایجاد گشتاور مورد نیاز دستگاهها هستند. در واقع، نیروی مورد نیاز دستگاههای صنعتی با استفاده از این قطعات تأمین میشود. بنابراین، میتوان آنها را قطعاتی مؤثر در انتقال نیرو معرفی کرد. با توجه به اهمیت عملکرد آنها در دستگاههای مختلف، نحوه انتخاب گیربکس به عنوان موضوعی مهم جهت راندمان یا کارایی مفید دستگاهها تلقی میشود. در این ارتباط، توجه به برخی ویژگیها میتواند در انتخاب قطعه ای متناسب با نیاز دستگاه مفید باشد. نوع محرک ورودی، توان ورودی و خروجی، دور ورودی و ضریب کاری گیربکس از جمله این ویژگیها هستند. در این مقاله انواع گیربکسهای صنعتی، با تأکید به برند آوکمن و کاربرد آنها را مورد بررسی قرار میدهیم.
- آشنایی با گیربکس های صنعتی
- انواع گیربکس صنعتی
- کاربرد گیربکسهای صنعتی
- اصطلاحات مربوط به گیربکس صنعتی
- انتخاب گیربکس صنعتی
- جمع بندی
آشنایی با گیربکس های صنعتی
در مقوله آشنایی با گیربکس های صنعتی، این قطعات به عنوان وسایل یا قطعاتی برای تبدیل انرژی و انتقال قدرت معرفی میشوند. در این قطعات، انتقال توان مکانیکی از منبع تولیدکننده (موتور) به مصرف کننده (دستگاه) اتفاق میافتد. به این ترتیب، سرعت و گشتاور مورد نیاز منبع مصرف کننده تأمین میشود. جهت کارکرد مفید این قطعات در دستگاههای صنعتی باید به گشتاور مورد نیاز دستگاه توجه شود .
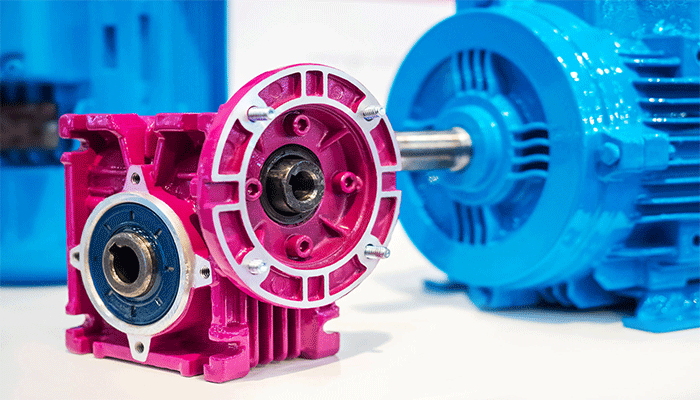
گیربکسها را میتوان قطعاتی برای هماهنگ کردن سرعت و گشتاور بین دو منبع موتور و دستگاه مورد نظر تعریف کرد. انتقال نیرو در گیربکسهای صنعتی از طریق شفت انجام میشود. توان تولید شده در موتور باید در شفت ورودی گیربکسها به صورت گشتاور منتقل شود. توان مورد نیاز گیربکسهای صنعتی را با استفاده از دستگاههای مختلفی میتوان تولید کرد. الکتروموتورها، موتورهای گاز سوز، بنزینی و دیزلی، انواع توربینها (گازی، بادی، آبی) و منابع تولید نیروی خورشیدی از جمله این دستگاهها هستند. اجزای تشکیل دهنده گیربکسها عبارتند از:
- چرخ دندهها
- پوسته گیربکس
- شافت ورودی و خروجی
- بلبرینگ
- کاسه نمد
انواع گیربکس صنعتی
از دیگر مقولههای مهم در حوزه آشنایی با گیربکس های صنعتی، بررسی انواع آن است. با توجه به نوع دستگاه و انتظارات تعریف شده از این قطعه، انواع مختلفی از گیربکسهای صنعتی معرفی میشوند. بنابراین، بهتر است تا پیش از هر چیز با انواع گیربکس صنعتی آشنایی پیدا کرد.
در یک دسته بندی کلی، گیربکسهای صنعتی به دو گروه افزاینده و کاهنده طبقه بندی میشوند. عملکرد نوع کاهنده این قطعات، افزایش گشتاور خروجی و کاهش سرعت است. در حالیکه، نحوه عملکرد گیربکس صنعتی افزاینده با کاهش گشتاور و افزایش سرعت معرفی میشود. گشتاور همان نیرویی است که باعث چرخش یک جسم حول یک محور میشود. در گیربکسهای مختلف با استفاده از فرمول محاسبه گشتاور خروجی گیربکس صنعتی میتوان این ویژگی را محاسبه کرد.
· گیربکس خورشیدی
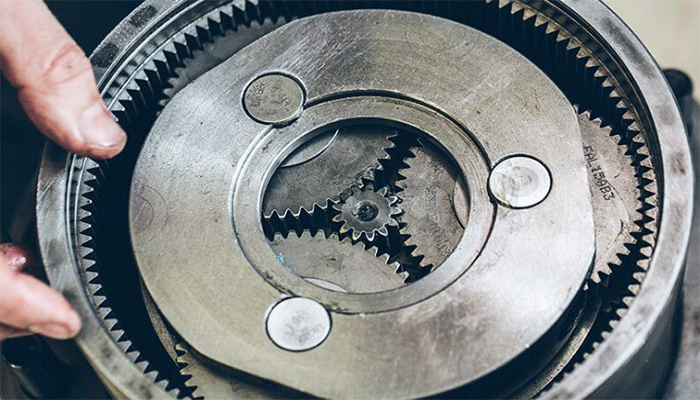
در حوزه آشنایی با گیربکس های صنعتی، نام گیربکسهای خورشیدی بیش از سایر انواع آنها به چشم میخورد. در این گیربکسها یک چرخ دنده در وسط و سه چرخ دنده در اطراف آن قرار گرفته اند. چرخ دنده وسط را خورشید و سه تای اطراف آن را سیارهها مینامند. برای دریافت بهترین عملکرد در گیربکس خورشیدی باید ویژگیهایی چون توان الکتروموتور، دور خروجی و تعداد دندانههای آن مورد توجه قرار گیرند. در این ارتباط، توان ورودی و خروجی گیربکس نیز پارامترهای مهم محسوب میشوند که با استفاده از فرمول محاسبه توان گیربکس قابل سنجش و ارزیابی هستند.
گیربکسهای خورشیدی در زمره پرمصرف ترین انواع این قطعات صنعتی به شمار میآیند. از مزایای این نوع گیربکس میتوان به قابلیت کاربری آنها در دورها و توانهای بالا اشاره کرد. راندمان، توان و دقت بالا، استحکام و دوام مناسب گیربکسهای خورشیدی از دیگر مزایای این گروه محسوب میشود. با استفاده از این نوع گیربکسها در دستگاههاسی صنعتی، عمر مفید آنها افزایش مییابد.
· گیربکس حلزونی کاهنده
این نوع گیربکسها به دلیل استفاده از یک چرخ دنده حلزونی با قطر زیاد به این عنوان نامگذاری شده اند. حرکت دورانی بخش حلزونی به عنوان عامل محرک یک چرخ دنده دیگر یا سایر قطعات محرک عمل میکند. عمده کاربرد این گیربکسها در صنایع سنگینی چون مواد شیمیایی، مواد معدنی و تولید کود تعریف میشود. با توجه به نسبت تبدیل متفاوت این گروه، لازم است تا انتخاب و خرید آنها با توجه به نیاز دستگاه انجام شود.
· گیربکس هلیکال
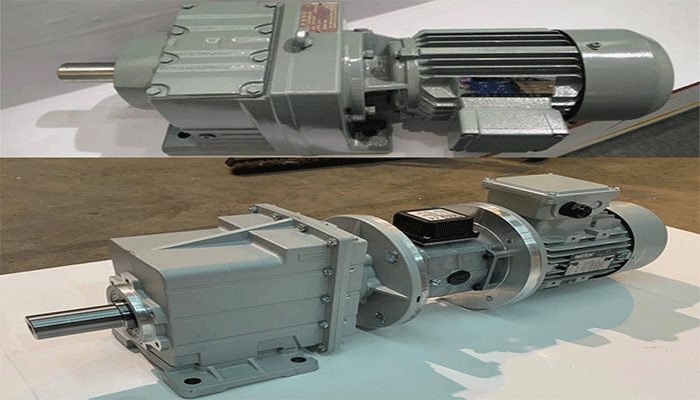
در زمینه آشنایی با گیربکس های صنعتی، نوع هلیکال برای بسیاری از صنعتگران بسیار پرطرفدار محسوب میشود. در گیربکسهای هلیکال، چرخ دندهها به صورت مارپیچی قرار گرفته اند. نحوه کار گیربکس صنعتی هلیکال افزایش گشتاور در قسمت خروجی با افزایش دور است. سایز کوچک، توان مصرفی پایین، حجم اندک و آلودگی صوتی پایین از جمله ویژگیهای مثبت گیربکسهای هلیکال است. علاوه بر این، عمر مفید این گروه از گیربکسها، به دلیل ساییده شدن اندک چرخ دندهها، در رتبه بالایی قرار میگیرد. گیربکس هلیکال را میتوان در زاویه ای خاص فیکس کرد. به طوری که حرکت دندانههای آن به صورت یکنواخت و در جهتی ثابت ممکن باشد. این حرکت یکنواخت برای یک پریود زمانی مشخص قابل تکرار است. موارد کاربرد این گروه از گیربکسها عبارت است از:
- کارخانههای تولید سیمان
- کارخانههای سنگ شکن
- صنایع تولید لاستیک
- پلاستیک سازی
کاربرد گیربکسهای صنعتی
انواع کاربرد گیربکس صنعتی یکی از روشهای نامگذاری این قطعه پرکاربرد است. به عبارت دیگر، با توجه به نوع کاربرد گیربکسهای صنعتی در صنایع مختلف، آنها را گروه بندی میکنند. بر این اساس انواع آنها را میتوان به صورت زیر دسته بندی کرد:
· صنعت تولید شکر
آشنایی با گیربکس های صنعتی قابل کاربری در صنعت تولید شکر جهت دریافت راندمان مناسب، اتلاف کمتر انرژی و افزایش درصد بهره وری مهم تلقی میشود. در این صنعت دو گیربکس خورشیدی و هلیکال گزینههای کاربردی معرفی میشوند. با استفاده از این نوع گیربکسها میتوان گشتاور و سرعت نیروی تولید شده توسط موتور را مدیریت کرد.
· فولادسازی
در صنعت تولید فولاد ویژگیهای مهمی چون قدرت و ظرفیت و دقت بالای گیربکسها مهم تلقی میشوند. با توجه به ویژگیهای ذکر شده، گیربکسهای خورشیدی و پینیون انواع مفید این قطعات برای صنعت فولادسازی معرفی میشوند. با کاربری این نوع گیربکسها میتوان عملکردی پایدار و حرکتی نرم را ایجاد کرد.
· سیمان سازی
در صنعت تولید سیمان از گیربکسهای بسیار قوی استفاده میشود که گشتاور زیادی را تحمل میکنند. از این رو آشنایی با گیربکس های صنعتی با ویژگی کارایی بالا در این صنعت ضرورت دارد. با توجه به اندازه و قدرت بسیار بالای موتورهای مورد استفاده در این صنعت، گیربکسهای هلیکال و شافت مستقیم انواع مفیدی در صنعت سیمان به شمار میآیند. با استفاده از این نوع گیربکسها میتوان از گشتاور تولیدشده در موتور بهترین خروجی را دریافت کرد.
· صنعت تولید کاغذ
به طور معمول در صنعت تولید کاغذ گیربکسها جهت کنترل نیرو و سرعت ماشین تولید کاغذ کاربرد دارند. گیربکسهای خورشیدی بهترین نوع این قطعات برای صنعت ذکر شده تعریف میشوند.
اصطلاحات مربوط به گیربکس صنعتی
برای خرید یک قطعه صنعتی لازم است تا درباره اجزای مختلف آن قطعه و عملکرد هر یک اطلاعات کافی داشت. این موضوع در مورد خرید گیربکسهای صنعتی نیز میتواند مفید باشد. بنابراین، بهتر است تا ضمن آشنایی با گیربکس های صنعتی درباره اجزا و اصطلاحات فنی این قطعه دانش کافی داشت.
شافت ورودی، شافت خروجی و نسبت تبدیل کل گیربکس از جمله آیتمهای قابل توجه در ارتباط با این قطعه صنعتی هستند. شافت ورودی بخشی از گیربکسهای صنعتی است که عملکرد آن به ورود نیرو از موتور به محفظه چرخ دندهها مربوط میشود. شافت خروجی نیز بخشی است که در انتقال قدرت نقش دارد. این شافت در مقایسه با شافت ورودی سرعت چرخش کمتری دارد.
نسبت تبدیل، کمیتی است که با توجه به دو ویژگی دور ورودی و خروجی گیربکس تعیین میشود. این کمیت از دو طریق قابل محاسبه است. در روش اول، نسبت تبدیل از طریق شمارش تعداد دندانههای چرخ دنده ورودی و خروجی محاسبه میشود. برای محاسبه این کمیت باید تعداد دندادنههای خروجی گیربکس را به تعداد دندانههای ورودی آن تقسیم کرد.
روش دوم محاسبه نسبت تبدیل با اندازه گیری قطر چرخ دنده ورودی و خروجی انجام میشود. در این روش هم باید قطر دندانه خروجی را به قطر چرخ دنده ورودی تقسیم کرد.
روش دوم محاسبه نسبت تبدیل با اندازه گیری قطر چرخ دنده ورودی و خروجی انجام میشود. در این روش هم باید قطر دندانه خروجی را به قطر چرخ دنده ورودی تقسیم کرد.
انتخاب گیربکس صنعتی
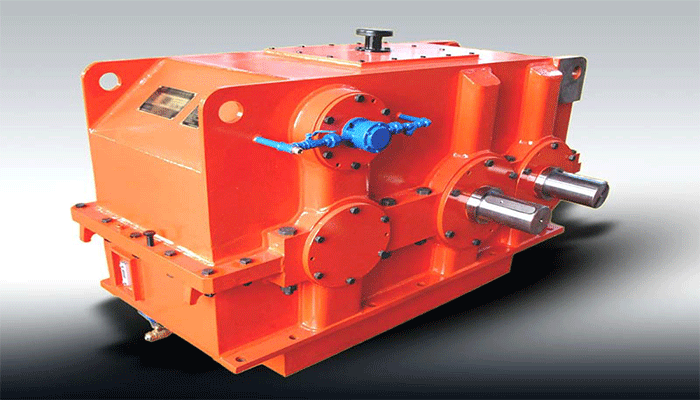
یکی از نکات مهم جهت افزایش راندمان و دوام و کارایی مفید دستگاههای صنعتی، انتخاب گیربکس مناسب است. در این گزینش پارامترهای زیر را باید مورد توجه قرار داد:
- توان مورد نیاز
- شرایط محیط کاری (رطوبت، دما)
- نوع ماشین مورد کاربرد
- مشخصات فنی موتور محرک
- آرایش محورهای انتقال قدرت
- نحوه انتقال دور بین گشتاور و موتور
در حال حاضر برندهای مختلفی در زمینه این قطعه صنعتی تولید و روانه بازار شده اند. موتور گیربکس آوکمن به عنوان یکی از برندهای برتری است که در ادامه توضیحات بیشتری درباره آن ارائه میدهیم.
معرفی گیربکس صنعتی آوکمن (Aokaman)
آوکمن یک برند چینی تولیدکننده انواع گیربکس، موتور و قطعات جانبی است. آوکمن از معتبرترین برندهای گیربکسهای صنعتی با رعایت استانداردهای جهانی محسوب میشود. موتور گیربکسهای این برند دارای گارانتی 18 ماهه و انواع گواهی نامههای بین المللی است. از ویژگیهای فنی این قطعه میتوان به گشتاور تولیدی 2600000-22 نیوتن متر و قدرت 12934-0.4 کیلو وات آن اشاره کرد.
شرکت مهندسی فن آوران رستاپاد به عنوان نماینده انحصاری این شرکت در ایران فعالیت میکند. این شرکت پیشرفته ترین گیربکسهای صنعتی در اندازه و ظرفیتهای مختلف را طراحی و اجرا میکند. کارشناسان این مجموعه با ارائه مشاورههای فنی شما را در انتخاب کارامدترین محصول مورد نیازتان همراهی میکنند. در رستاپاد خدمات پس از فروش و خدمات بازرسی محصول در حین ساخت و پس از آن ارائه میشود.
جمع بندی
به منظور درک بهتر عملکرد دستگاههای مختف در کارخانجات و صنایع مختلف، آشنایی با گیربکس های صنعتی ضروری است. با توجه به تنوع این قطعه صنعتی، جهت انتخاب درست آنها باید پارامترهای ذکر شده در این مقاله مد نظر قرار گیرند. برای دریافت کارکرد حداکثری گیربکس بهتر است این قطعه به صورت مورد بررسی و بازبینی قرار گیرد. در این حالت ضمن رفع نقص و آسیبهای احتمالیوارد شده با آن، میتوان بهترین راندمان را از قطعه دریافت کرد.
1- گیربکس صنعتی چیست؟
گیربکس صنعتی قطعه ای جهت انتقال نیروی مکانیکی از یک منبع تولید به یک مصرف کننده جهت تأمین گشتاور و سرعت مورد نیاز آن است.
2- پارامترهای مهم در انتخاب گیربکس مناسب کدامند؟
توان مورد نیاز، شرایط محیط کاری (رطوبت، دما)، ، نوع ماشین مورد کاربرد، مشخصات فنی موتور محرک، ارایش محورهای انتقال قدرت و نحوه انتقال دور بین گشتاور و موتور
3- انواع گیربکس صنعتی کدامند؟
گیربکسهای صنعتی شامل گیربکس خورشیدی، حلزونی و هلیکال هستند.