معرفی بهترین نقاط کشور برای کارخانه آهن اسفنجی (بخش سوم: از نظر دسترسی به منابع انرژی)
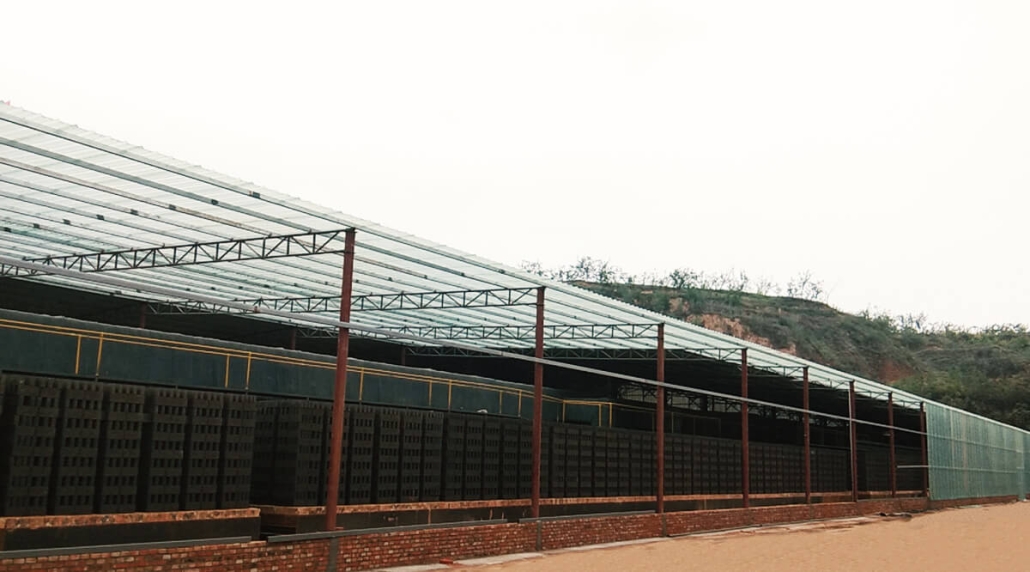
از جمله هزینه هایی که میزان سوددهی یک طرح تولیدی را تحت تأثیر قرار می دهد، هزینه های مصرف انرژی است. انتخاب موقعیت جغرافیایی مناسب برای دسترسی بهتر به انرژی، حتی اگر در کوتاه مدت حایز اهمیت نباشد، از هزینه های تحمیل شده در دراز مدت جلوگیری می کند. این هزینه ها میتواند ناشی از عدم اشراف به شرایط منابع انرژی، و یا سیاست های منطقه ای و دولتی در آن منطقه باشد.
در احداث کارخانه کوره تونلی نیز، نحوه و فراوانی دسترسی به مواد مصرفی از اهمیت بسیاری برخوردار است. مواد مصرفی جاری در این فرآیند را می توان به دو دسته کلی مواد اولیه و حامل های انرژی تقسیم بندی نمود.
قبل از هر چیز این را بگوییم که در مطلب “بهترین موقعیت جغرافیایی برای احداث کوره تونلی (از نظر مواد اولیه آهن دار)“ به شرایط دسترسی به مواد پایه آهن دار در سطح کشور برای استفاده در فرآیند احیاء مستقیم پرداختیم. توصیه میکنیم اگر نخواندهاید ابتدا آن مطلب را مطالعه نمایید.
همچنین، دو ماده مصرفی دیگر در روش کوره تونلی، شامل زغال حرارتی و پودر سنگ آهک است. در مطلب “بهترین موقعیت جغرافیایی برای احداث کوره تونلی (از نظر فراوانی زغال و آهک)“ هم به شرایط دسترسی به این مواد در نقاط مختلف کشور پرداختهایم.
اما در مطلب پیش رو، به دسته دیگر مواد مصرفی، یعنی حامل های انرژی می پردازیم. در طرح تولید بریکت آهن اسفنجی به روش کوره تونلی، حامل های انرژی مورد استفاده شامل گاز طبیعی، برق و آب می باشند. بنابراین دسترسی به زیرساخت های مناسب تأمین این انرژی ها، از بسیاری از هزینه های آتی پیشگیری خواهد کرد.
منابع تأمین گاز طبیعی
بر اساس نمودار زیر، به منظور تحقق چشم انداز سال 1404 برای تولید 55 میلیون تن فولاد خام، سالانه حدود 18.7 میلیارد مترمکعب گاز نیاز است که از این میزان، تولید آهن اسفنجی با اختلاف، بیشترین مقدار مصرف موردنیاز را به خود اختصاص داده است [1]. برای غلبه بر این چالش، در طرح جامع فولاد راهکار استفاده از تکنولوژی هایی مانند تولید هیدروژن با منابع تجدیدپذیر در مرحله تولید آهن اسفنجی پیشنهاد شده است.
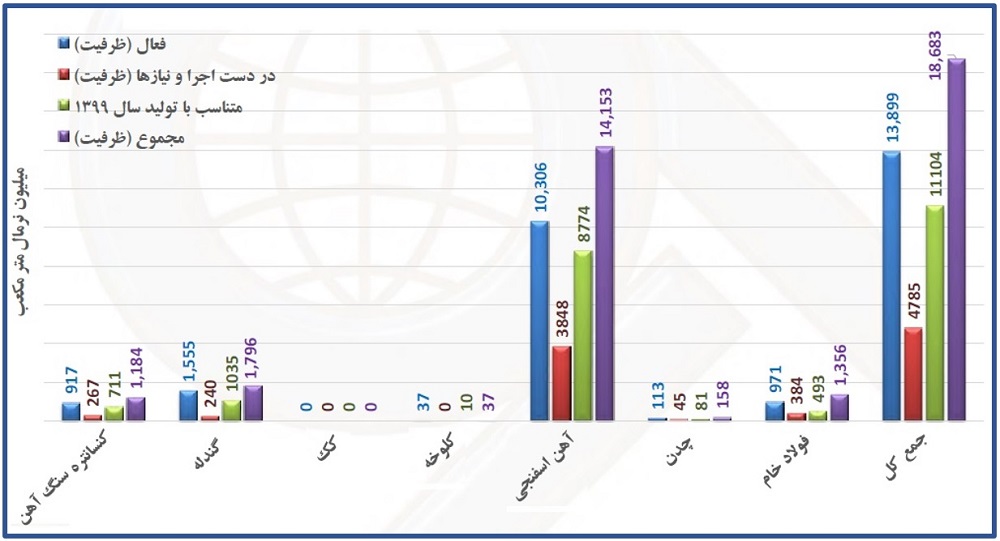
متأسفانه توسعه خطوط انتقال گاز با برنامه های توسعه فولاد همگام نبوده است و ظرفیت انتقال در برخی از خطوط کشور ناکافی است. یازده خط انتقال اصلی در ایران در حال اجرا و بهره برداری است که عمده آنها در جنوب و غرب کشور پراکنده شده اند [1]. البته توسعه خطوط گاز در استان سیستان و بلوچستان در دو محور شمالی و جنوبی (خط هفتم) در حال انجام است. با نهایی شدن طرح صادرات گاز به هند و پاکستان، تعداد ایستگاه های تقویت فشار خط هفتم چندین برابر خواهد شد [1].
بنابراین، این منطقه پتانسیل بالایی برای توسعه صنعت فولاد در آینده خواهد داشت. هم اکنون نیز، مجتمع فولاد مکران در چابهار با ظرفیت تولید 3.2 میلیون تن فولاد خام آماده بهره برداری است و مطابق با افق 1404، ظرفیت تولید این منطقه 10 میلیون تن برآورد شده است.
نقشه زیر، اولویت مناطق از نظر دسترسی به خطوط گاز را نشان می دهد که باید در انتخاب منطقه مناسب برای اجرای طرح های صنعت فولاد مدنظر قرار گیرد [1]. مشاهده می کنید که مناطق جنوبی ایران برای اجرای طرح هایی با مصرف گاز بالا، بیشترین اولویت را دارند.
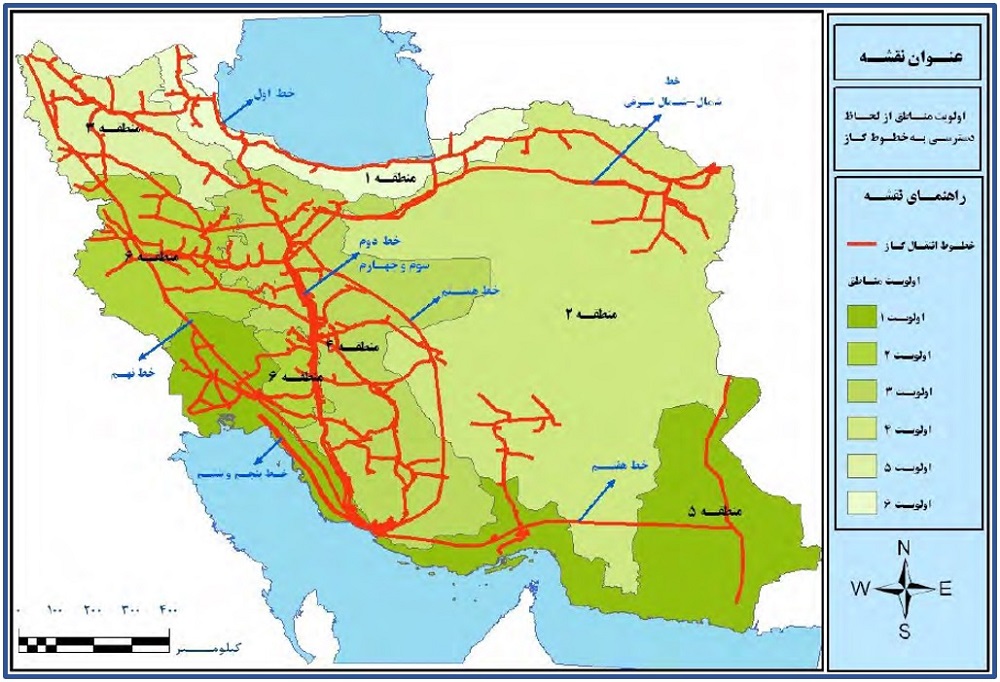
منابع تأمین برق
مطابق با پژوهش طرح جامع فولاد، رشد متوسط سالانه مصرف برق در صنعت فولاد حدوداً 40% بیشتر از رشد متوسط ظرفیت نیروگاه ها در کشور می باشد [1]. دلایل این موضوع را می توان در عدم وجود سرمایهگذاری، تغییر قیمت ارز، تحریم و محدودیت منابع آبی جهت احداث نیروگاه های جدید دانست.
بر اساس نمودار زیر، به منظور تحقق چشم انداز سال 1404 برای تولید 55 میلیون تن فولاد خام، سالانه حدود 46 میلیون کیلووات ساعت برق نیاز است که از این میزان، بیشترین گلوگاه مصرف به تولید فولاد خام اختصاص دارد [1]. پس از آن، تولید آهن اسفنجی حدود 12% مقدار مصرف را به خود اختصاص داده است. برای غلبه بر کمبود برق، در طرح جامع فولاد راهکارهایی مانند احداث نیروگاه های برق به عنوان بخشی از سرمایه گذاری واحدهای فولادی، و استفاده از تکنولوژیهای نو و منابع تجدیدپذیر پیشنهاد شده است.
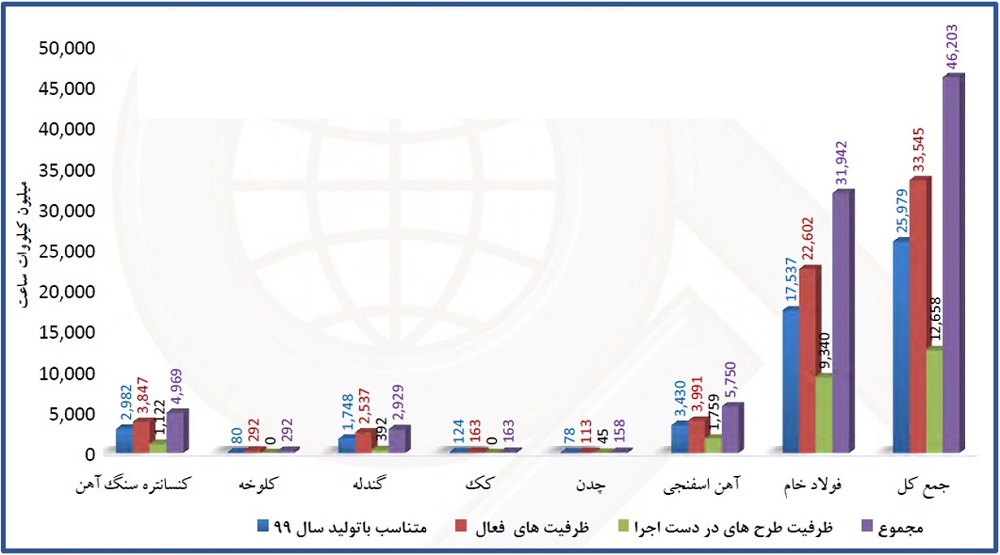
نقشه زیر، اولویت مناطق از نظر دسترسی به خطوط انتقال برق را نشان می دهد که باید در انتخاب منطقه مناسب برای اجرای طرح های صنعت فولاد مدنظر قرار گیرد [1]. مشاهده می کنید که مناطق شرقی و مرکزی ایران بیشترین اولویت را دارند.
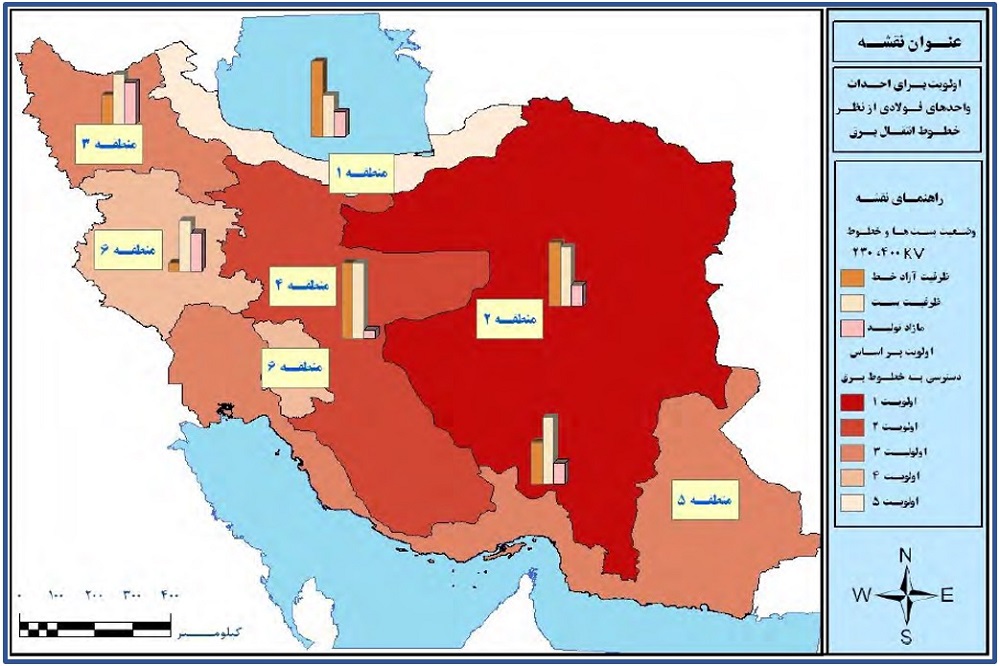
منابع تأمین آب
متأسفانه در زمان تهیه این مطلب، با خشکسالی شدید در بسیاری از مناطق کشور و ممنوعه شدن دشت ها از نظر اجازه برداشت آب روبرو هستیم. به طوری که طی سال های گذشته، مرتباً به تعداد دشت های ممنوعه جهت پیاده سازی طرح های عمرانی و صنعتی افزوده شده است و حتی مناطق ساحلی شمال و جنوب کشور نیز، با خشکسالی خفیف مواجه بوده اند. نقشه و نمودار زیر این وضعیت را به خوبی ترسیم می کند [1]:
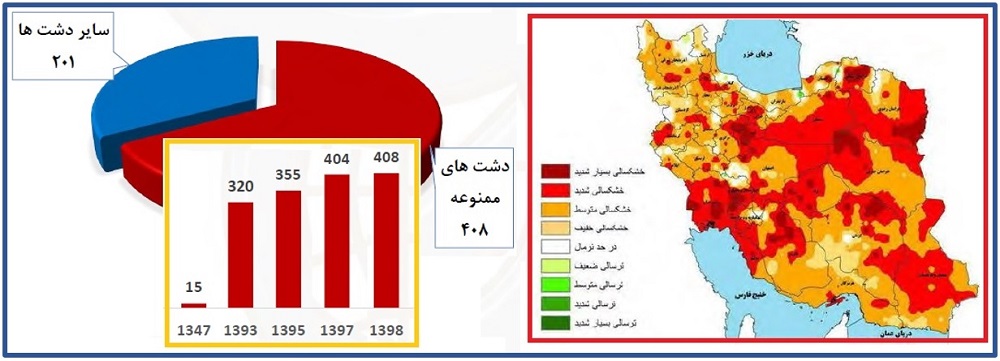
در نمودار زیر، میزان مصرف آب در صنعت فولاد نشان داده شده است که حدود 0.2% از کل مصارف کشور می باشد [1]. هر چند این مقدار، در مقایسه با سایر بخش ها ناچیز به نظر می رسد، لازم است برای به حداقل رساندن آن از راهکارهای مناسب و به روز استفاده شود.
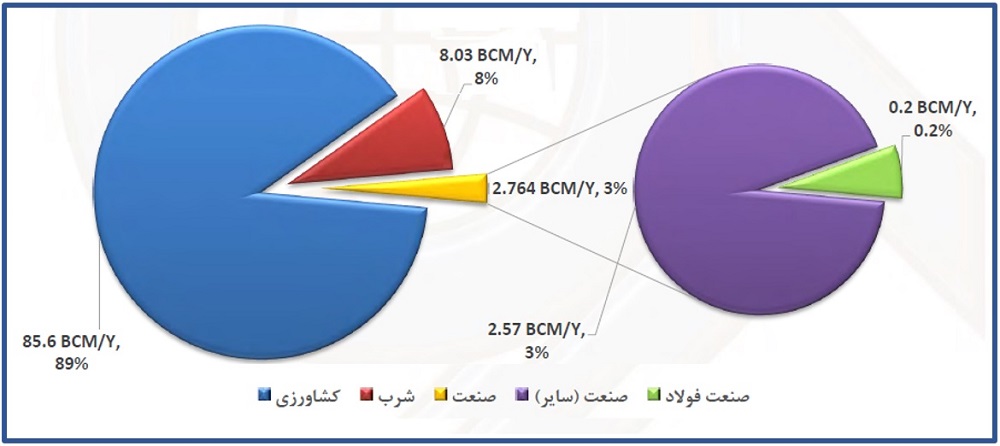
راهکارهای معرفی شده در پژوهش جامع فولاد ایران سال 1399، به قرار زیر است [1]:
- احداث واحدهای جدید فولادی در مجاورت سواحل جنوبی کشور
- استفاده از فن آوری های فولادی کم مصرف آب
- بهره گیری از روش های کاهش مصرف آب (خنک کننده های هوایی، برج خنک کننده هیبریدی، غبارگیرهای خشک)
در این راستا، بهترین مناطق برای احداث کارخانجات فولادی مطابق با نقشه زیر تعریف شده است [1]. مشاهده میکنید که مناطق جنوبی کشور، بیشترین اولویت را برای اجرای طرح هایی با مصرف آب بالا دارند.
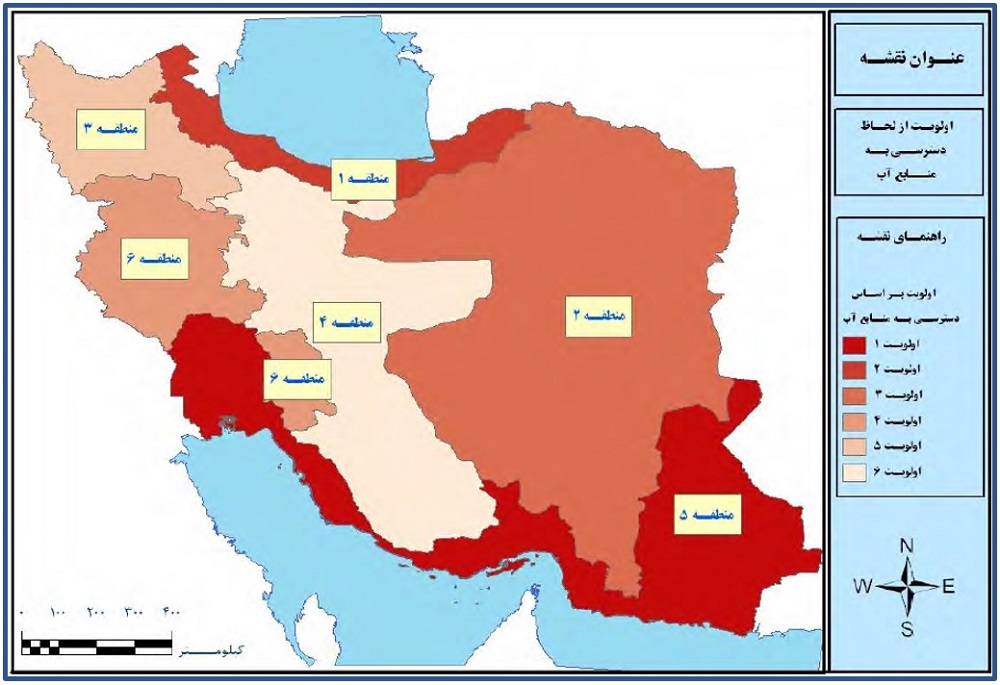
در همین پژوهش، کل مصرف سالیانه آب در زنجیره فولاد در سال 1404، برابر با 253 میلیون مترمکعب پیش بینی شده و پراکندگی این مقدار در مناطق شش گانه کشور، مطابق با نقشه زیر معین شده است [1]:
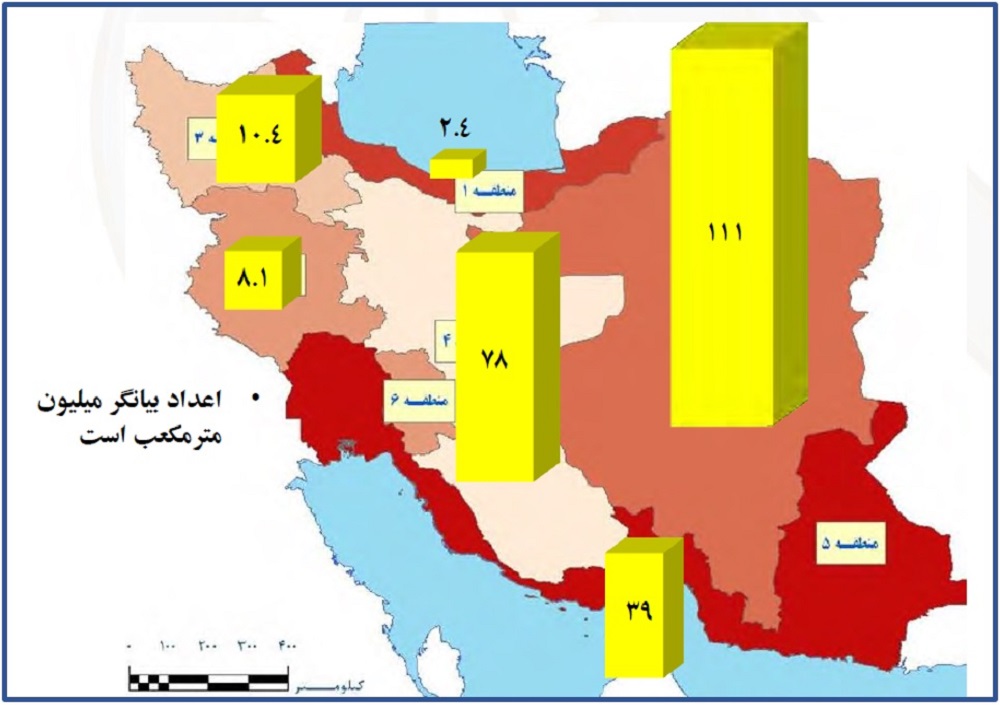
از میان رقم پیش بینی شده، 57 میلیون مترمکعب آن برای تکمیل طرح های دست اجرا و تکمیل زنجیره تعریف شده، که تنها 8% از این مقدار به واحدهای در حال احداث در مجاورت سواحل جنوبی اختصاص دارد [1].
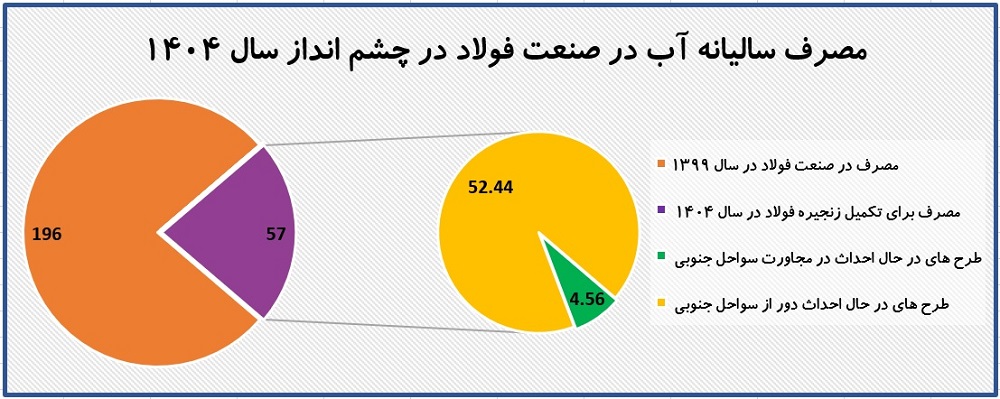
به همین دلیل، برای استان های غیرمجاور با دریای جنوب، دو راهکار جهت دسترسی به آب معرفی شده است:
- استفاده از پساب تصفیه شده شهرها
- شیرینسازی و انتقال آب به مناطق مرکزی کشور
برای تصفیه پساب شهرها، پروژههایی در تعدادی از استان های مرکزی در حال جریان است. برای مثال، در استان اصفهان، تصفیه خانه هایی برای استفاده مجتمع های فولاد مبارکه، ذوب آهن اصفهان، و پالایش نفت اصفهان در حال انجام است. پروژه های مشابهی نیز در استان های البرز و همدان برای تأمین آب اضطراری صنعت و کشاورزی مطرح شده است.
همچنین، برای شیرین سازی و انتقال آب دریای جنوب، طرح های زیر در نظر گرفته شده است:
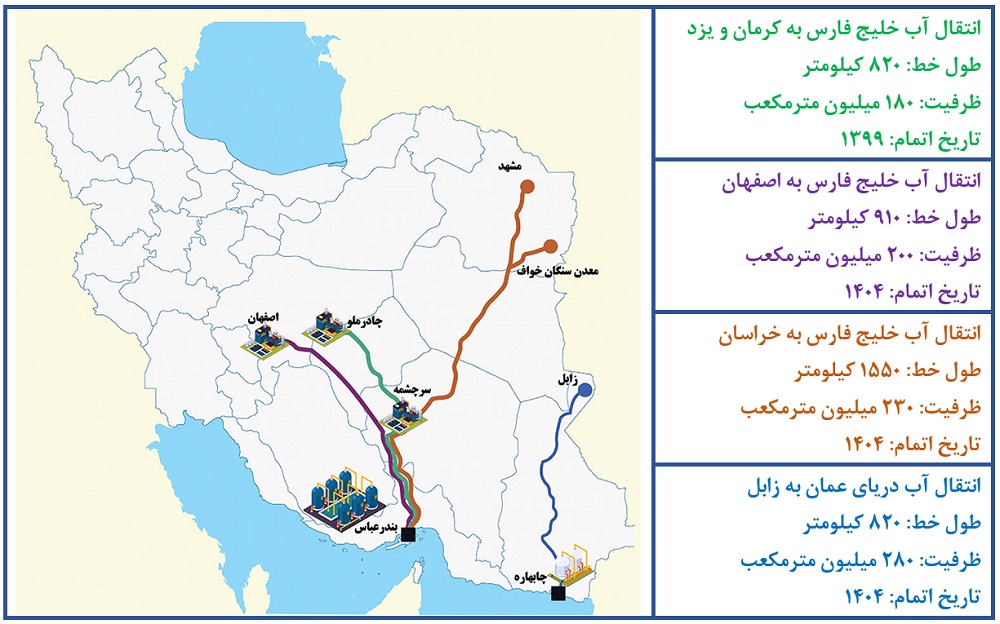
تأمین انرژی های موردنیاز در طرح کوره تونلی
با توجه به آن چه تاکنون مطرح شد، می توان به طور کلی نتیجه گیری کرد که در احداث واحدهای صنعت فولاد، استان های جنوبی از لحاظ دسترسی به منابع گاز و آب، در اولویت هستند. از طرفی در دسترسی به برق، مناطق شرقی و مرکزی ایران شرایط بهتری دارند. با این وجود، درباره روش کوره تونلی باید به این نکته توجه کنیم که این طرح در زنجیره گسترده فولاد، یک روش کوچک-مقیاس تولید آهن اسفنجی به شمار می آید.
بنابراین، در ظرفیت های پایین مدنظر در این روش، وضعیت منابع انرژی در سطح کلان چندان مطرح نیست. البته روشن است که کارآمدی هر طرح تولیدی را باید در کل سال های بهرهبرداری آن سنجید. به علاوه، بهتر است احتمال اجرای طرح های توسعه در آینده را درنظر بگیریم. به همین دلیل، داشتن دید بلندمدت به تأمین انرژیهای مصرفی، در انتخاب بهترین موقعیت های جغرافیایی اهمیت دارد.
از بین حامل های انرژی مورد نیاز در کارخانه کوره تونلی، دسترسی به گاز طبیعی بیشترین اولویت را داراست و پس از آن تأمین برق در مرتبه دوم اهمیت قرار دارد. در مقایسه با بسیاری از فرآیندهای صنعت فولاد، مصرف آب در این روش پایین بوده و به عنوان عاملی تعیین کننده درنظر گرفته نمی شود. بنابراین می توانیم نتیجه بگیریم که بهترین مناطق احداث این کارخانه از نظر دسترسی به حامل های انرژی، مناطق جنوب شرقی ایران و در حدفاصل استان کرمان با خراسان جنوبی، سیستان و بلوچستان و هرمزگان قرار دارد.
شرکت مهندسی فن آوران رستاپاد مجری طرح تولید آهن اسفنجی به روش کوره تونلی
در این مقاله سعی کردیم از بین عوامل مؤثر بر مکان یابی برای احداث کارخانه کوره تونلی، شرایط تأمین انرژی های مصرفی را بررسی کنیم. موارد بسیاری در این مکان یابی موثرند که مهم ترین آن ها شرایط تأمین مواد اولیه است. همچنین وضعیت حمل و نقل برای انتقال مواد اولیه و فروش محصول و امکان پیاده سازی طرح های توسعه کارخانه در آینده را باید درنظر گرفت.
بنابراین، اگر علاقمند به دریافت اطلاعات بیشتری در این زمینه هستید، با کارشناسان ما تماس بگیرید. در نظر داشته باشید، شرکت مهندسی فن آوران رستاپاد نماینده انحصاری شرکت OTSK، تنها بهرهبردار موفق تولید آهن اسفنجی به روش کوره تونلی در ایران است.
منابع:
[1] مطالعات طرح جامع فولاد کشور (پایش سال 1399)، شرکت ملی فولاد ایران